Table Of Content

The return rollers are selected based on their spacing, the weight of the belt per unit length, and belt tension. During the selection process, it’s common to return to the initial capacity calculation and vary the belt width or speed to arrive at a workable design. In operations with many conveyors, standardization of components is often desired, which may affect component selection. The size and shape of lumps on the belt is an important design limitation as well. Rather than stop production, the belt runs full speed, and chute blockages and spillage result.
Tonnage per Hour Production Requirements
The automated nature of conveyor belts means that workers don’t have to manually handle large items or lift heavy loads while they work. This improves safety on the production floor, reducing the risk of accidents and injuries. For modern warehouses, manual transfer operations are unable to keep up with throughput levels required for speedy order fulfillment cost-efficiently.
How much do conveyor systems cost?
Roller conveyors are commonly used in warehouses, distribution centers, and assembly lines. Join us as we unravel the secrets behind maximizing production output through optimal conveyor belt design. This new edition continues on its journey of being an introduction to the wide variety of conveyor types and application methods available.
Top Conveyor Belt Manufacturers and Suppliers in the US & Canada - Thomas Insights
Top Conveyor Belt Manufacturers and Suppliers in the US & Canada.
Posted: Fri, 27 Oct 2023 07:00:00 GMT [source]
What Are Conveyor Systems?
Hatch Launches Design Software for Pneumatic Conveying Systems - Powder Bulk Solids
Hatch Launches Design Software for Pneumatic Conveying Systems.
Posted: Fri, 10 Nov 2023 08:28:11 GMT [source]
Dynamic weighing conveyors can be used in any industry or application where weight needs to be controlled or monitored. They can be used to monitor total produced product or to control raw product feed to a production process, based on what the product recipe requires. In order to design the most effective system we need to understand exactly what it is it needs to transport.
If objects are particularly heavy or bulky — or if the conveyor belt is carrying them for a long distance or duration — rollers may be placed on the sides of the conveyor belt for support. A conveyor belt works by using two motorized pulleys that loop over a long stretch of thick, durable material. When motors in the pulleys operate at the same speed and spin in the same direction, the belt moves between the two. The point where items are transferred to and from the conveyor is a critical one. Most conveyors use side to side transfers, powered transfers, dead plates, gravity rollers, etc. to facilitate this. Products with a smaller footprint may require a powered transfer, while larger and longer products may need gravity rollers.
In some industries, a conveyor belt brings products through a manufacturing or packaging line and back out again. A large plastic chain conveyor is best used for transferring plastic-footed pallets, while a chain-driven roller conveyor is best suited for wooden pallets. Also, the former is best used for moving smaller boxes or totes than the latter. Factors such as product weight, dimensions and fragility will greatly impact your decision process.
By monitoring productivity metrics, such as units produced per hour or labor hours per unit, manufacturers can identify opportunities for process optimization and performance improvement. Automated conveyor systems can collect real-time data on production output, downtime, and performance metrics. This data can be analyzed to identify bottlenecks, optimize workflows, and make data-driven decisions to improve overall manufacturing efficiency. Automated conveyor systems can be integrated with sensors, scanners, and other technologies to ensure accurate and precise material handling.
Call Designed Conveyor Systems
To the material handling equipment and systems experts likeus here at Kemper Equipment, the simple question, “how should I design my conveyor system? You should keep a constant watch over your conveyor design to see if there are any improvements that could be made to the system. Designed Conveyor Systems offers continuous support to previously-installed systems. There is always something that can be improved upon with the advice from an experienced conveyor design expert. Conveyor system design doesn’t need to be quite as strict if motors are to be used. This allows for inclines and corners to be utilized as the materials move from one section of the facility to the next.
Conveyor Systems – The Fundamental Building Blocks of Warehouse Automation
Sortation conveyors are widely used in picking, packing, manufacturing, receiving, and shipping. Powered by sensors, software, and mechanical sorting devices, these conveyors can send products to different destinations. When you’re setting up a new aggregate processing operation,you may not know your production requirements at first. You can explore ourprevious post featuring materialcalculators & aggregate processing tech resources to help you, or justgive us a call here at Kemper Equipment to consult and create an optimizedproduction plan. Well, as we’ve said in the past, no two aggregate or mineralprocessing sites are quite alike. The wide variety of possible challengespresented by moving diverse materials frequently calls for advanced solutionsthat only conveyorsystem customization can address.
Conveyor systems are mechanical devices used to transport various items with minimal manual effort from employees. Although there are a wide variety of specifics involved with conveyor systems, the general construction will be similar. A frame will create a track and support a means of moving materials from one area to the next – perhaps rollers, a belt, or wheels. A conveyor system is a fast and efficient mechanical handling apparatus for automatically transporting loads and materials within an area. This system minimizes human error, lowers workplace risks and reduces labor costs — among other benefits. They are useful in helping to move bulky or heavy items from one point to another.
A vibratory conveyor system moves materials from one location to another using vibration to facilitate the movement. The surface of the conveyor is usually a smooth metal trough, improving durability and allowing for conveyance of hot materials. The trough is attached to a network of reactor springs and a drive connection situated on an angle causing the trough to vibrate and facilitate the material to move in the desired direction. There are different types of vibrating conveyors which can be classified based on the design and type of application. Additionally, the E3.series offers tools to support the diverse variations of conveyor system design.
While conventional conveyor systems such as moving walkways and grocery store conveyors are straight, sometimes, the unit needs to turn to deliver the items to the proper location. For the turns, there are unique cone-shaped wheels or rotors which allow the belt to follow a bend or twist without getting tangled. In a production line, conveyors will not only expedite the procedures but also increase plant productivity. Slat ConveyorsSlat conveyors can be used for assembly applications because they can be loaded and unloaded using robotic automation. They are similar to belt conveyors in the sense that their smooth surface prevents damage or harm to items being moved. Gravity Roller ConveyorsGravity roller conveyors are a set of rollers connected to a side frame.
It is very similar to belt conveyors, but it uses a chain mesh instead of a rubber belt. The chain mesh makes it a poor choice for fragile materials, but they are a low maintenance way to transport heavier loads or to transport items through rough elements like the heat of a pizza oven. They do consume more power, so they are sometimes reserved for applications that a rubber belt may not be suitable for. While there are numerous types of conveyor systems, all serve the same purpose of transporting materials. Some products may require a system without a belt, using only rollers or wheels for flexible movement. However, many conveyor systems rely on a frame with a belt and possible support rollers to carry materials and products efficiently.
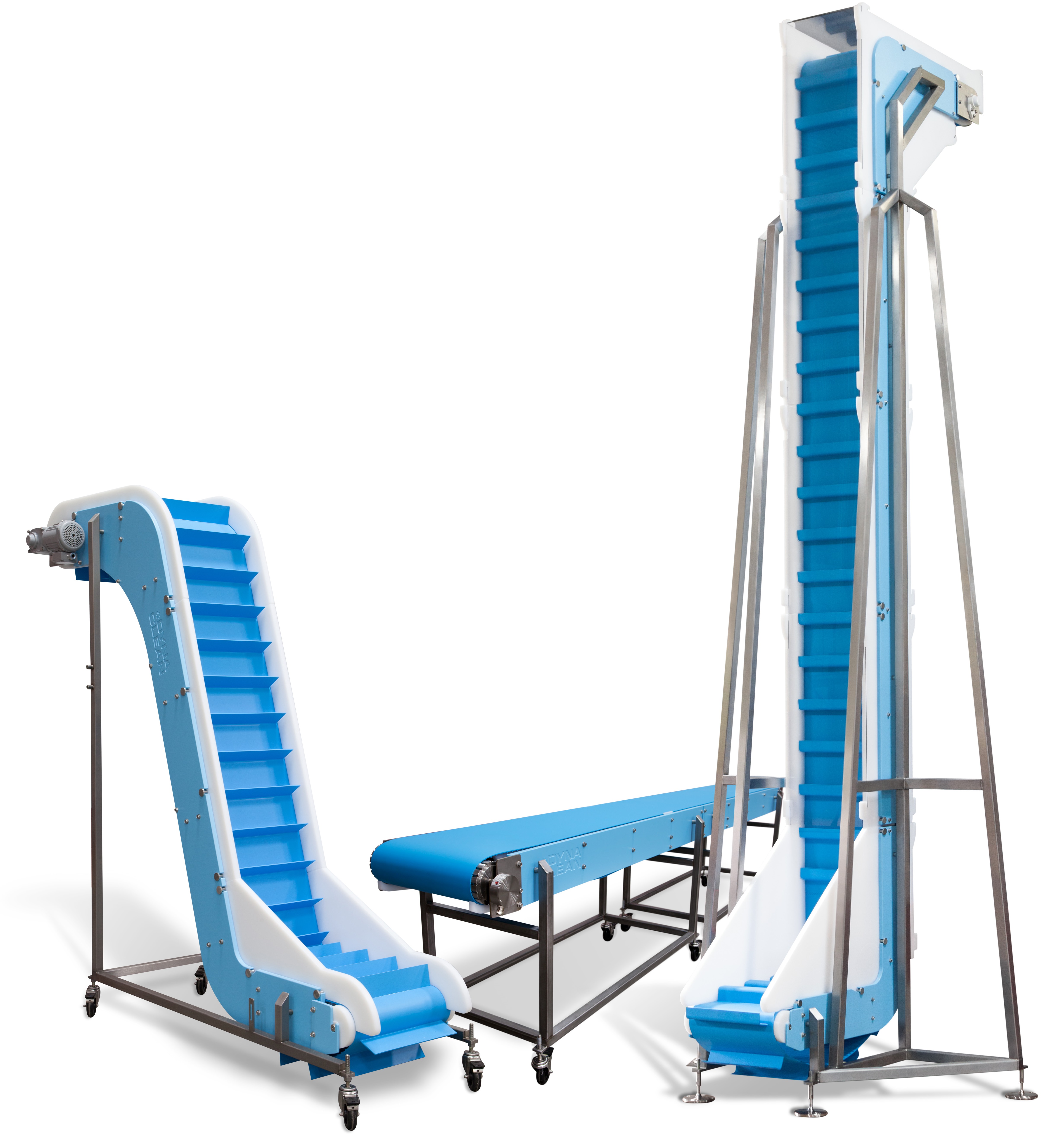
It consists of a friction drive, load bearing track, switch, stopper, trolley, elevator and steel structure with the major benefit of operating cleaner and quieter. Skid ConveyorSkid conveyors move products on fixtures with longitudinal runners called skids. Screw ConveyorsScrew conveyors move bulk substances such as granular products and loose materials. A screw conveyor's central part is a rotating helicoid on a shaft inside a pipe.
Understanding the different types of conveyor belts and their applications allows manufacturers to select the most suitable option for their specific production needs. Choosing the right conveyor belt type ensures smooth material handling, reduces product damage, and maximizes overall production output. Conveyor belts are the lifeline of any production process, seamlessly transporting materials from one stage to another. The right design ensures smooth movement, prevents unnecessary downtime, reduces product damage, and improves overall throughput. From food and beverage to automotive and mining, every industry relies on conveyor belts to maintain operational flow. Delving into the realm of belt conveyor system design unveils a complex yet fascinating process that combines engineering principles with practical applications.
No comments:
Post a Comment